The ANSI/ASSE Z244.1 – 2003 (R2008) standard also addresses other lockout techniques, called alternative methods of controls. These systems can save costs and improve machine up time. But alternative methods controls only apply to routine, repetitive tasks that are integral to the production process and are based on risk assessment providing effective personal protection. The machine must still have a standard lockout system for repairs and other tasks.
Alternative methods of controls offer two-time saving advantages. First, it uses a single lock-point (a remote, low-voltage system) that simplifies and speeds lockout, and enhances safety by avoiding the chance of a point being missed. The operator need not travel all around the machine to access various points to lockout or unlock operations. These systems place electrical lockout switches, connected to the control system, at locations that require machine access, and incorporate appropriate safety valves for pneumatic and hydraulic lockout.
The second feature of alternative lockout systems is not all energy needs to be removed. In fact, sometimes removing all the energy creates a more-hazardous condition. This can result in significant time and cost savings when systems contain large volumes of compressed air.
The standard is also useful for tasks that are not routine, repetitive, or integral to production, but require power for, say, troubleshooting a control circuit. The new standard recognizes that there is no such thing as zero risk, and that some risk is present in order to perform certain tasks. In this case, the standard requires that the control system and valve controlling the non-isolated energy be control-reliable, Category-3 or -4.
Helping You With Machine Safety or Machine Guarding as it Has Become Known
ROSS employs a team of Global Industry Specialists with vast experience in fluid power applications with special emphasis on SAFETY. Scattered around the globe, the ROSS Safety Team participates on industry standards committees that set policy and best practices for machine guarding. Most people (in the U.S.) have heard of and are quite familiar with OSHA. However, many would be surprised to learn that OSHA laws are based on the technical recommendations of many specific industry or standards organizations, such as the Robotics Industry Association (RIA), the Packaging Machinery Manufacturers’ Institute (PMMI), the American National....
ROSS® Safety Applications
-
Energy Isolation
Pneumatic Energy Isolation is achieved with a manually operated valve in a system that stops the further input of a specific energy. Isolation devices for pneumatic systems are generally used in conjunction with a bleed device that is used to dissipate energy that may be downstream of the isolation device. In most pneumatic devices, the isolation device and bleed device are combined into a single component that shuts off the supply of pneumatic energy and also exhausts downstream pneumatic energy from as far downstream as possible.
Learn MoreHere are some simple design guidelines from the safety standards to keep in mind when setting up your pneumatic lockout and energy isolation system:
- The energy isolation device should be unique in appearance compared to other ON/OFF devices
- The energy isolation device should dump hazardous energy quickly
- The energy isolation device should only be lockable in the OFF position
- The system should include a visible indication of a safe condition
Interested in Energy Isolation? See What We Have To Offer!
Browse Our CatalogHow do ROSS Lockout Valves match Design Guidelines?
- Unique Appearance – Easily identifiable with a yellow body and a red handle to control ON/OFF positions
- Quick Energy Dump – Full size exhaust ports (equal to or larger than supply) are included to enable the lockout valves to dump downstream energy quickly
- Lockable Position – Design only allows the valve to be locked out in the OFF position
- Visible Indication – Includes integrated sensor port for pressure verification with either a visual pop-up indicator or electrical pressure switch
-
Safety Exhaust
A safe manufacturing environment must include a healthy respect for the, sometimes dangerous, interactions between man and machinery. This is reflected in the evolution in the once simple and now sophisticated safety-related valves. In pneumatic and hydraulic circuits where the primary concern is the removal of pneumatic or hydraulic energy from a device or system, additional dump or exhaust valves are typically incorporated specifically for this function.
Learn MoreThe function of a Safety Exhaust Control Valve mimics that of an electrical control relay and is subject to the same rules for classifying safety integrity. Properly specified machine safeguarding systems include provisions for pneumatic valves including:
- Must be functionally redundant
- Must be monitored for faults (including diminished performance faults which may create the loss of redundancy) without depending on external machine controls or safety circuitry
- Must return to a safe position in the event of a loss of pressure or other such event
- Able to inhibit further operation upon detection of a fault until it is corrected
Interested in Safety Exhaust? See What We Have To Offer!
Browse Our CatalogHow do ROSS Reliable Safety Exhaust Double Valves match Design Guidelines?
- Redundant – Includes dual internal valves
- Monitoring – Includes a self-contained dynamic monitoring system requiring no additional valve monitoring controls
- Safe Position – Valve will shift to a locked out position whenever the valve elements operate in an asynchronous manner
- Fault Condition – Reset can only be accomplished by the integrated electrical reset and cannot be reset by removing and re-applying supply pressure or electrical power
-
Safe Cylinder Return
ROSS CrossMirror Double Valves provides control reliable cylinder/actuator control resulting in increased safety and savings.
Learn MoreTypical safety designs look to remove the air to a machine or zone. If there is a single actuator hazard it can be controlled with a safety control valve providing point of use control. This provides not only safety but offers savings in air consumption and eliminates any downtime due to recharging the system.
The CrossMirror valve is internally self-monitored and requires no additional valve monitoring controls. It also includes a status indicator switch (ready-to-run) to inform machine controller of the valve condition. This switch must be integrated into machine controls in order to prevent a run signal until the valve fault is cleared.Interested in Safety Exhaust? See What We Have To Offer!
Browse Our CatalogThese valves are used in a variety of applications including cylinder presses, potentially hazardous filling applications where spilling is not an option, and critical clamping applications.
-
Load Holding
Cylinder applications must take into consideration what happens with the loss of air pressure and how will impact the safety of both man and machine. This is especially important with vertical cylinder applications.
Learn MorePilot Operated Check Valves, otherwise known as PO Checks, are used wherever a high-flow or remotely controlled checking function is needed to provide cylinders to automatically stop in the event of the loss of electrical power or system air.
A pilot operated check valve is designed to trap pressure and hold a load in place. The design provides a positive force using the force of the trapped pressure to help hold the internal poppet seat in place. The trapped pressure will need to be exhausted safely to resume normal machine operation.Interested in Safety Exhaust? See What We Have To Offer!
Browse Our CatalogIn addition to single and dual valve options, ROSS India 27 Series PO Check Valves are offered with manual and remote trapped pressure relief options to provide a safe exhaust function.
A Global Snapshot of Fluid Power & Safety
Critical-application safety valves are functionally redundant, self-monitoring, and return to a safe position. It is easy to say that “Safety is everyone’s goal,” but what is really meant by that? Sound workplace safety practices can reduce the risk of injury to not only machine operators but to other people such as maintenance technicians; it can also reduce the risk that there is accidently damage to machinery and other company assets, or harm to the environment. Common industry standards acknowledge that there is no such thing as zero risk, while nonetheless providing guidance to machine builders and operators regarding how to take steps to minimize risks. This is commonly referred to as a machine safeguarding. Here’s a snapshot look at some key factors:
-
Alternative Lock-out
-
Risk Reduction
There is no such thing as “zero risk”. Therefore, the standards require that you assess all possible risks, and determine what possible ways can be accomplished for most-effectively reducing those risks. The best approach to risk assessment is as a team. One big change ANSI B11.TR3-2000 brought about is that both the machine manufacturer and user are responsible for performing the assessment for new and rebuilt machines. In the past, machine safety was considered the user’s responsibility. Perhaps the most difficult part is defining the subjective words for the assessment. There are no precise answers, and even the standards differ. Users need to develop their own risk assessment program.
Many companies hold that there are two degrees of injury: minor and major. Minor injuries can be treated with a first aid kit, and anything requiring more extensive care is considered a major injury for risk assessment purposes. When a company uses a risk matrix that leans toward the “better-to-be-safe” side, the first question is, of course, “Will it entail additional expense to eliminate a rare possibility?” But to error on the high side forces the assessment team to look more carefully at each hazard. Often, safety can pay back in machine up time, reduced employee absenteeism, saving the time and cost to investigate an accident, insurance savings, and other hidden costs involved with accidents. Safety is part of a company’s loss-prevention program.
Avoiding using the wrong category valve should be the primary concern when performing a risk assessment. For example, a circuit with a single valve that suffers a broken spring or a sticky spool would have a different fault result than a similar circuit employing a double valve experiencing a broken spring or sticky valve. ANSI B11.TR3-2000 sets the recommended minimum level of control integrity as follows.
- Highest degree of risk reduction - Control systems having redundancy with continuous self-checking to ensure continuous performance.
- High/intermediate risk reduction - Control systems having redundancy with self-checking upon startup.
- Low/intermediate risk reduction - Control systems having redundancy that may be manually checked.
- Lowest degree of risk reduction - Hydraulic or pneumatic devices and associated control system using single-channel configuration.
-
Path to Safety
The path to fluid power safety can be taken with these 6 steps:
- Identifying tasks and hazards using a Risk Assessment with fluid power considerations.
- Classify these hazards into categories from slight to serious, seldom to frequent, and possible to less possible.
- Reduce the risk by a Risk Reduction Hierarchy from Preferred to Fifth.
- Select the appropriate controls for safeguarding.
- Assess the Residual Risk.
- Record actions taken, monitor results, and document.
-
Safety Circut Examples
- Cylinder hazard in 2 directions
- Pinch Points
- Tooling or product damage
- Single Point Lock Out
- Press clutch/brake
- Counterbalance
- Monitored power systems
- Partial de-energization
- Vertical loads
- Cylinder hazard in 2 directions
- Cylinder mid-stroke positioning
- Two-hand control
- Energy Isolation
- EEZ-ON gradual pressure build-up
- Noise reduction
- 2-hand anti-tie-down machine start
- Hose and/or fitting failure
Additional Resources:
Ross India Offers and expanded technical reference book "Fluid Power Safety for Machine Guarding", and a course in Fluid Power Safety, "TOTAL MACHINE SAFETY".
Design Standards and Certifications:
ROSS valves for Safety-related applications are designed to meet many Global standards including the following: CSA, Australian AS, EN, ISO, OSHA, ANSI, & CE
When required, ROSS products can be tested and certified by the following authorities: UL, CSA, TUV, BG
Safety Integrity Software Tool for the Evaluation of Machine Applications (SISTEMA)
ROSS India is pleased to announce the free download of its safety product data library designed for use with the innovative new Safety Integrity Software Tool for the Evaluation of Machine Applications (SISTEMA). Developed by the Institute for Occupational Safety and Health of the German Social Accident Insurance (IFA, formerly known as the BGIA), SISTEMA is available to download currently for no charge at the IFA website. This software tool is expected to prove invaluable to system designers because of its potential time savings and safety implications. Click the link below to get started.
Get Started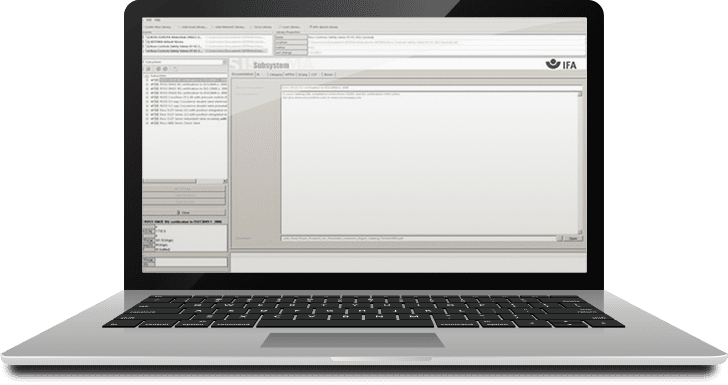
ROSS India - White Papers
Allowing you and your employees to be safe in the workplace requires attention to risk assessment, machine design, equipment functionality, employees, technicians, continual assessment of these assets, and continual education in best safety practices. Machine safeguarding and making safety first is everyone’s goal, and you can take advantage of additional free resources to make that happen. ROSS is proud to provide downloadable white papers for you to use to increase the safety in your business and stay up to date on industry standards. You can find all the latest white papers by clicking the link below.
View White PapersTotal Machine Safety™ Course
Total Machine Safety is the first fully-integrated electrical and fluid power machine safeguarding training program. This comprehensive approach to evaluating and designing safety control systems is critical to the overall success of your safety program. In addition, when you address machine safeguarding early in the machine design process you begin to realize that safety is just good business.
Get StartedContact Our Team
ROSS employs a powerful team of experts with vast experience in fluid power able to help you find a solution for your safety goals. Whether it be a custom solution, a current product, application, or safety course, ROSS is here to provide just what you need with your business specifications in mind.